Un proyecto innovador, pionero en el país y que es ejemplo de sostenibilidad ambiental es la planta de transformación de llantas usadas, ubicada en el centro del Cesar. Es una solución para la problemática que se presentaba por el desuso de estos elementos cuyo diámetro alcanza los cuatro metros.
“Esta iniciativa lo que busca es dar disposición adecuada a cada una de las llantas que se generan en el corredor minero. Sabemos que son llantas realmente gigantes y que tienen una gran cantidad de material que podemos volver a utilizar en la industria”, dijo el ingeniero mecánico, especialista en mantenimiento Industrial y director de Planta de Duramos, Jesús Libardo Maurello Vaca, quien precisó que es un proyecto realmente nuevo, pese a que el montaje se hizo en diciembre del 2020, el primer motivo de arranque fue en 2021.
La razón de ser de este proyecto es tener un impacto ambiental realmente considerable devolviendo a la cadena de suministro lo que es el tema del caucho y también acero a gran escala y acero en forma de viruta, preciso el Ingeniero Maurello.
Se trata de llantas OTR (Off The Road), “fuera del Camino” de rines 24 hasta llegar al 63 que son las más grandes del mercado mundial.
La planta funciona al interior del complejo de explotación minera Drummond y la operación está a cargo de la empresa Duramos SAS y lo que hace es debilitar la llanta para poder procesarla.
Actualmente en esta planta se están procesando llantas ring 57 cuyo diámetro puede oscilar entre 3 metros 70 u 80 centímetros y con un peso entre 3.800 kilogramos dependiendo del desgaste. Tienen una gran cantidad de material disponible para reutilizar.
Las empresas mineras en Colombia reportaron entre 2017 y 2019 el uso de más de 18 mil llantas OTR, si a esto se le suma las llantas pequeñas y medianas que se desechan se estima una cifra que supera las 20 mil unidades, las cuales sin un correcto aprovechamiento se convertían en una problemática ambiental.
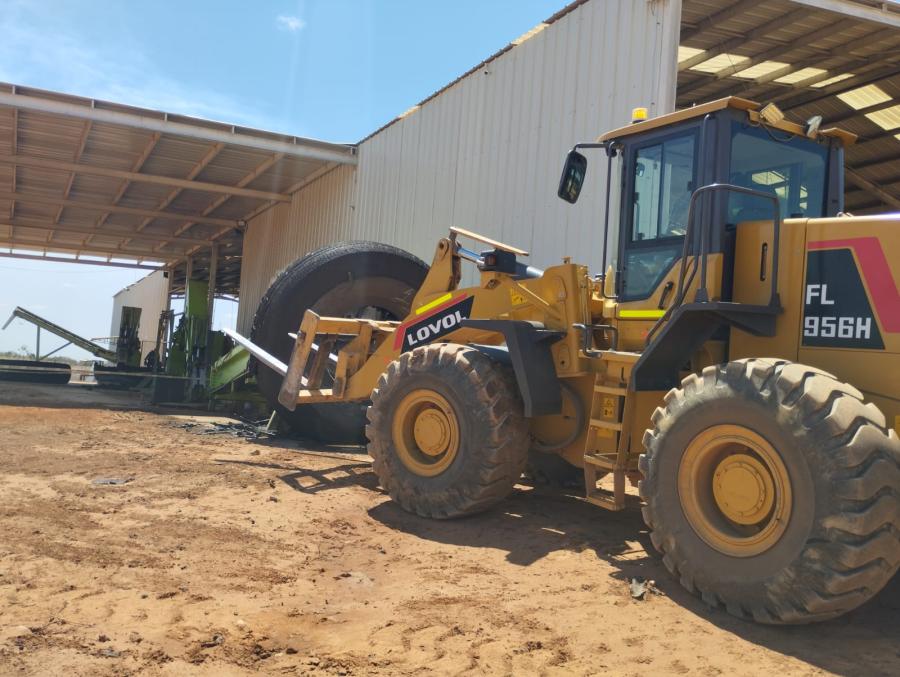
“La importancia ambiental de esta planta radica en que estas llantas están compuestas básicamente de tres materiales: el caucho, un acero grueso o solido grande que es que se utiliza en el talón, o un acero trenzado que es el que poseen en los cinturones que luego se tritura y sale en forma de vitura”, precisó el ingeniero.
Te puede interesar:
La idea es que con esta tecnología que llegó al país se vuelva a tener no solo un recurso o un pasivo ambiental acumulado, sino que esto vuelva nuevamente a la cadena de suministro ya que con caucho y acero se tiene un gran potencial de impulsar la economía de trabajar en la economía naranja o economía circular.
¿Cómo funciona la planta de trituración mecánica de llantas usadas?
Cuando la llanta llega al taller es revisada y se le extraen las piedras que puedan dañar las cuchillas de las máquinas, luego se montan en unos ejes y dos cuchillas giran a altas revoluciones y se posicionan sobre la llanta empezando a desgarrar trozos de la misma. En este proceso se le quita aproximadamente una tonelada de peso a la llanta.
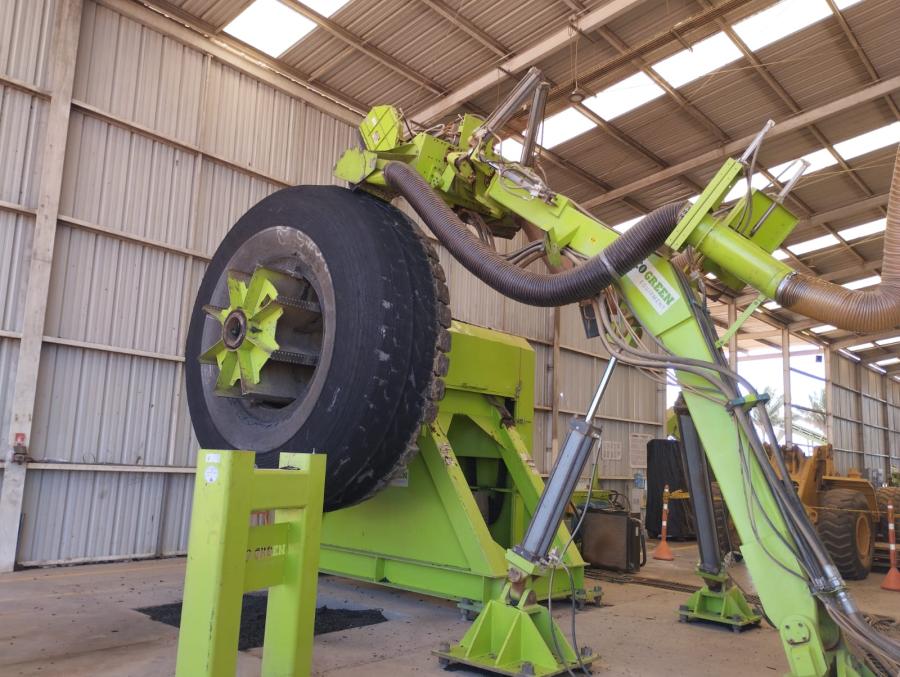
Ese primer proceso se llama proceso de raspado. Se utiliza una máquina que se llama Eco Razor, es electrohidráulica que la acciona un operador y va raspando la llanta en toda su totalidad.
Luego se pasa a la extracción de acero pesado, se hace con un gancho accionado por dos cilindros hidráulicos que halan el centro de la llanta y se recuperan entre 280 a 300 kilogramos de acero.
Se pasa a la tercera fase que es la fase de corte. Allí la llanta se vuelve puros cuadros con una máquina que es un Eco Shear que básicamente es un dinosaurio mordiendo la llanta y sacando secciones cuadradas.
Entonces, posterior a eso se pasa a trituración primaria y secundaria y se obtiene diferentes tipos de caucho o diferentes tipos de mallas o granulometrías. La planta puede procesar alrededor de ocho diferentes tipos caucho y dos tipos de acero.
Los productos se están vendiendo para utilizar en temas de jardinerías y en la industria nacional para hacer parques, bujes, empaquetaduras, sprocket, soportes de cabina, canchas sintéticas y hay planes pilotes para usar como asfalto modificado que es agregar al asfalto común caucho y esto aumentaría su capacidad de durabilidad, indicó el ingeniero Maurello.
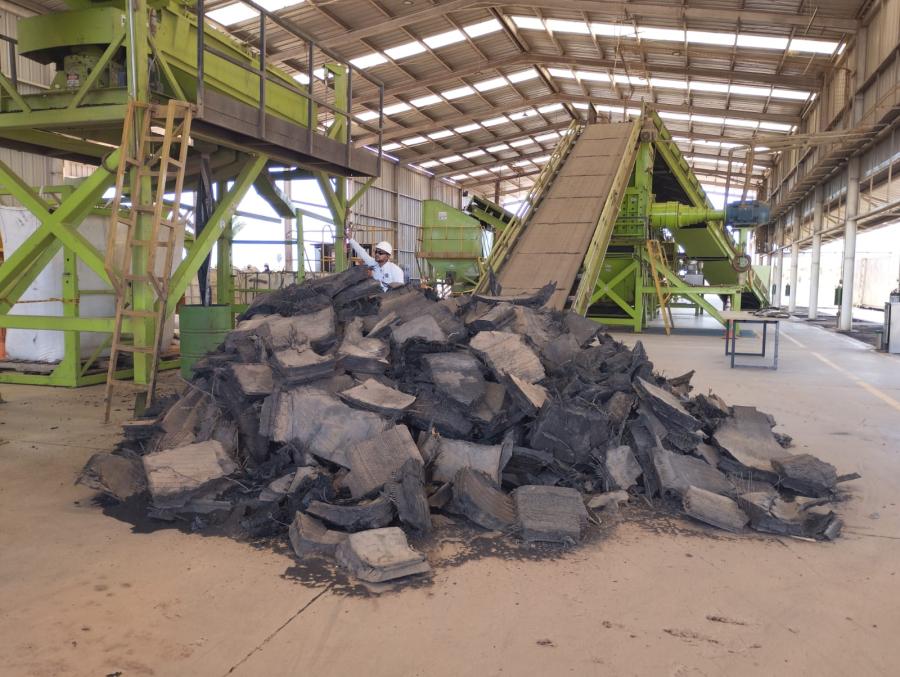
La planta está trabajando 24 horas al día. Aproximadamente se han procesado 8 millones de kilogramos entre caucho y acero. En el proyecto laboran directamente 30 personas y de manera indirecta entre 100 y 120, por lo que es considerado un proyecto pionero en América Latina.